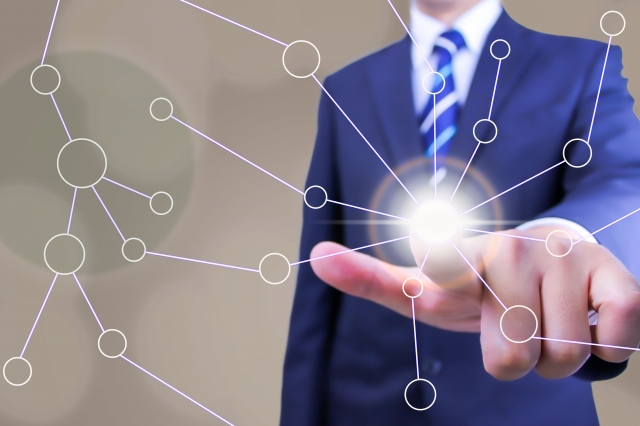
IoTの活用は、単なる技術導入にとどまらず、企業の業務効率化やコスト削減といった経営課題の解決に大きく貢献しています。
本記事では、IoTを導入し年間4億円のコスト削減実現した製造業の実例をご紹介します。
「費用対効果が見えない」「現場が反発しそうで不安」そんな悩みを抱えるあなたに向けて、IoT導入のメリット・デメリットはもちろん、実際の成功事例、よくある失敗例、導入ステップ、費用の目安までを網羅的に解説しています。
特に、100万円以下から始められるPoC(概念実証)の具体例を紹介し、現場の生産性を“数字で”改善するノウハウについてもお伝えします。
「IoT=コスト」ではなく、「IoT=利益を生み出す投資」として活用する方法を、今すぐチェックしてください。
1. IoT導入を迷う中小企業の経営者が抱える3つの代表的な悩み
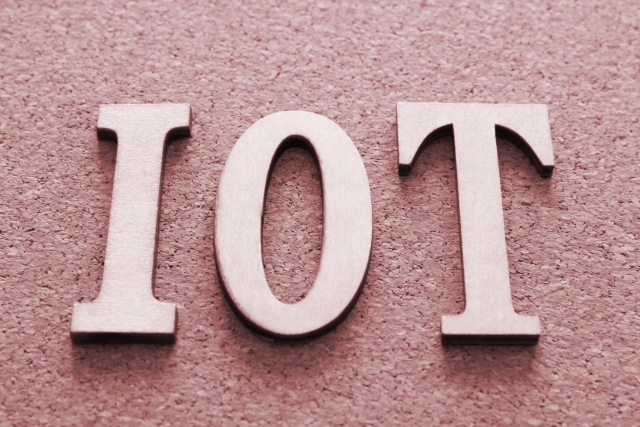
中小企業の経営者がIoT導入を検討する際に、共通して抱える悩みがあります。費用対効果への不安、社内体制への不安、そして自社への適合性への不安など、これらの不安を解消しない限り、IoT導入は絵に描いた餅に終わってしまいます。
まずは、IoT導入に際して経営者が抱える不安とそれに対する解決策についてご紹介します。
「ウチみたいな会社でもIoTで効果が出るのか?」
実は、少人数で回す中小企業こそ、IoTの恩恵を大きく受けられます。
たとえば、工場にセンサーを設置すれば、設備の稼働状況を“見える化”し、故障予知や業務のムダ削減が可能に。
大切なのは、自社の課題にIoTがどう活きるかを具体的に考えることです。その一歩が、利益改善につながります。
「費用対効果が見えない…何年で元が取れる?」
費用に見合う効果が本当に出るのか。これはIoT導入を迷う経営者に共通する悩みです。しかし、実際には数十万〜のスモール導入で、数年以内に回収できるケースも多くあります。
また、IoTを導入する場合は初期費用だけでなく、維持費・人件費削減効果まで含めた“全体コスト”で判断することが重要です。
まずは100万円以下のPoC(概念実証)で、効果を見える化するのがおすすめです。
「現場が対応できるか不安。社員が反発しないか心配」
せっかく費用をかけたのに、現場が使いこなせなかったり新しい仕組みに社員の反発が起こったりしたら、余計に生産性が落ちるのではないか。そんな不安もIoT導入でよく上られます。
だからこそ大切なのは、現場を巻き込むこと。導入前に丁寧な説明や研修を行い、社員の声を取り入れることで、スムーズな運用につながります。
「作業負担の軽減」や「スキルアップの機会」といったメリットを伝えれば、協力的な空気も自然と生まれるでしょう。
2. なぜ今、製造業・中小企業に「IoT導入」が必要なのか?その背景と課題とは
IoT導入は、生産現場を“データで見える化”することで、これまで見過ごされてきた課題をあぶり出し、改善につなげることが可能になります。では、具体的にどのような効果があるのでしょうか?
「生産性向上」「コスト削減」「新たな価値の創出」の3つのカテゴリに分けて見ていきましょう。
生産性向上|設備のムダを見える化し、効率を最大化
IoTによって、機械や設備の稼働状況をリアルタイムで把握できるようになると、ダウンタイムの原因や工程のボトルネックが明確になります。その結果、生産プロセスを最適化し、現場全体の生産性を大きく向上させることが可能になります。
コスト削減|人件費やエネルギー消費のムダを抑制
稼働状況の可視化により、非効率な運転や不良品の発生などの“隠れコスト”を抑えられます。さらに、人手に頼っていた管理業務の一部が自動化され、作業効率が向上。電力消費量の最適化によって、エネルギーコストの削減にも直結します。
品質向上と新たな価値創出|データで顧客満足を高める
製品ごとの品質データを収集・分析することで、製造ミスやばらつきの原因を特定しやすくなります。これにより品質の安定化が可能に。また、顧客の利用状況をもとに新サービスや製品改善につなげる「データ活用型の製品開発」も実現できます。
これらの効果を最大限に引き出すには、自社の現場に合ったIoTの仕組みを作ることが欠かせません。次章では、実際にこうした成果を出した企業の事例をご紹介します。
【実例公開】IoT導入で年4億円のコスト削減!自動車部品メーカーがが挑んだ“工場DX”の全貌
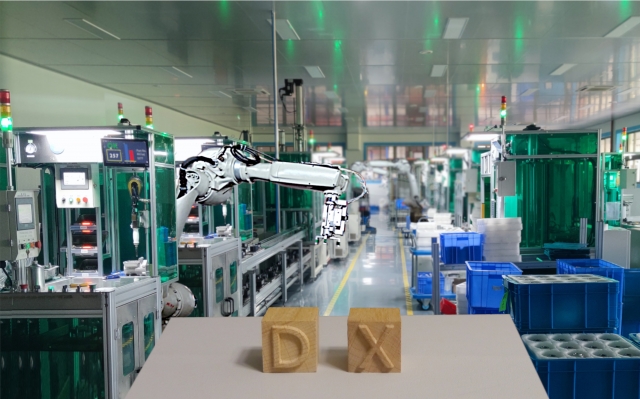
ある自動車部品メーカーでは、IoTとデータ活用によりわずか1年で年間4億円ものコスト削減と43%の生産性向上を実現しました。
「中小企業でもここまでできる」ことを証明したIoT導入の全プロセスを、導入前の課題から成果まで、順を追って紹介します。
導入前の課題:無駄な稼働、手作業の記録、残業増
ある自動車メーカーでは、長年の現場力と熟練工の勘に支えられた“属人的な生産管理”が主流でした。
しかし、設備の稼働状況や生産進捗がリアルタイムに把握できず、現場では多くのムダが発生していたのです。
【具体的な課題】
- 設備稼働の無駄:停止・待機時間が把握できず、機械がムダに動き続ける
- 手書きの記録:生産データは手作業で記録・集計され、正確性やスピードに課題
- 残業の常態化:進捗が見えず、非効率な管理が現場の長時間労働につながる
これらの状況が電力コストの増大・労働環境の悪化・人件費の増加を引き起こし、企業全体の競争力にも影を落としていました。
導入のプロセス|“安く・小さく・自社で”始めたIoT化
いきなり全社展開せず、まずは1台のプレス機からIoT導入をスタートしました。
既存設備に後付けできる安価なセンサーを活用し、初期費用を抑えながら効果検証を行う「スモールスタート」を徹底しています。
導入プロセスは以下の通りです:
1.プレス機にセンサーを取り付け:稼働・停止・振動などの状態をリアルタイムで取得
2.クラウドでデータを集約・可視化:専用ダッシュボードで稼働状況を“見える化”
3.社内ITチームで内製運用:外部業者に頼らず、システム構築や分析も自社で実施
この内製体制の構築こそが、低コスト・高速改善・現場密着型のDXを可能にしたポイントです。高額な外注に頼らず、自社の人材でノウハウを積み重ねたことで、継続的な改善につながりました。
導入後の成果|たった1年で年4億円削減・生産性43%向上
IoT導入からわずか1年。劇的な業務改善とコスト削減を実現しました。
最初に稼働監視を行ったプレス機では、ムダな稼働時間を43%削減。これを全社的に展開した結果、以下のような成果が得られました。
【主な成果】
- 生産性向上:+43%(稼働のムダ排除・進捗の可視化による効率改善)
- 人件費削減:約2億円/年(残業削減・手作業の記録作業を自動化)
- 電力コスト削減:約2億円/年(不要な稼働やアイドルタイムの排除)
- 初期投資:約1億円 → 投資回収期間:約1年未満
これらの成果はすべて、「既存設備にセンサーを付けただけ」「外注せず内製で運用」といった低コスト・現場起点の工夫によって達成されました。
大企業ではなく「中小製造業でもここまでやれる」それを代表的に示した企業の取り組みとなりました。
4. 中小企業でもできる!IoT導入を成功に導いた3つの戦略
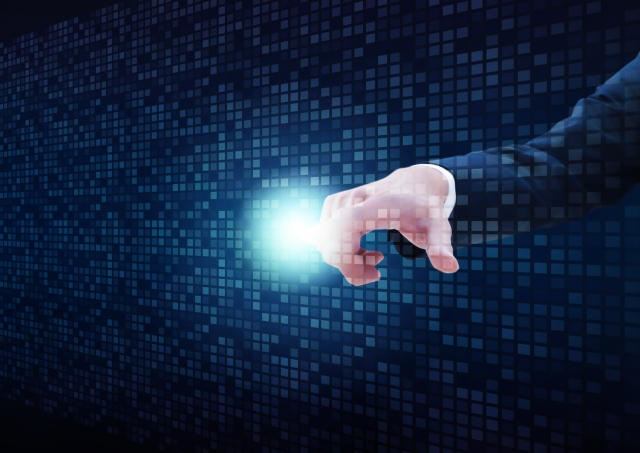
ここまで自動車部品メーカーの事例をご紹介しましたが「やっぱりウチで導入には無理かも」と不安になる必要は全くありません。実は、IoT導入に成功している中小企業の多くが、高額な投資も専門知識も不要な“現実的な戦略”を実践しています。
過去の事例に学ぶことで、どんな企業でも再現できる「始め方のコツ」が見えてきます。
ここでは、コストを抑えながら効果を最大化した3つの戦略をご紹介します。
戦略①|PoC(概念実証)で小さく始めて効果を見極める
いきなり全社導入するのではなく、まずは一部の製造ラインや機械にセンサーを取り付けてPoC(概念実証)を実施するのが成功の第一歩。
ある自動車部品メーカーでも、最初は1台のプレス機に温度や稼働状況を測定するセンサーを設置し、100万円以下の低コストで効果を検証しました。小さく始めて、成果を確認してから広げる。これが失敗しない鉄則です。
戦略②:高額システムではなく「既存設備×センサー」で十分
IoTと聞くと高額なシステム導入を想像しがちですが、既存設備にセンサーを後付けするだけで十分な効果が得られます。
自動車部品メーカーでは、既存の工作機械にセンサーを取り付け、稼働状況や電力使用量を可視化。高額な投資なしで生産性向上とコスト削減を実現しました。
戦略③|“現場主導型DX”でスムーズな定着を実現
IoT導入を成功させるカギは、現場の理解と協力です。今回紹介した自動車部品メーカーの事例では、導入前に現場の声を丁寧にヒアリングし、使いやすさを重視したシステムを選定。さらに、定期的な勉強会を通じて現場のITスキルも向上させ、無理なく定着させました。現場を巻き込むことで、導入後の形骸化を防ぎます。
この3つの戦略によって、年間4億円のコスト削減を実現することができました。中小企業でも、正しい手順を踏めば無理なく成果を出せることがこの事例からもわかりますね。
5. 中小企業向け IoT導入ステップ【PoC〜本格運用までの流れ】
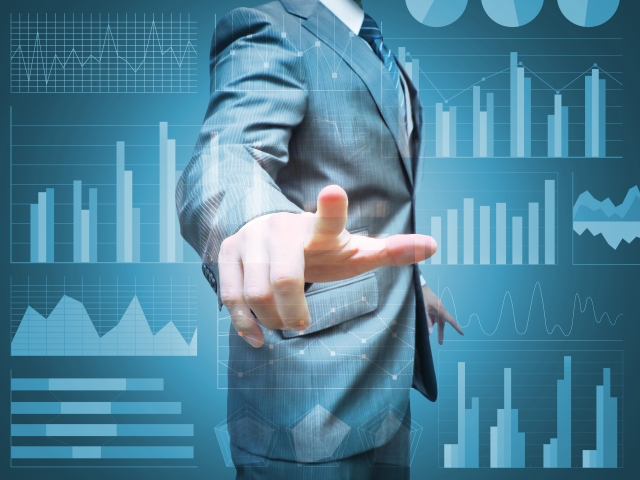
IoTの導入をやるべきなのは分かっているけど、どこから手をつければいいのかがわからないというという疑問も出てくるのではないでしょうか。
この章ではPoCから全社展開までの具体的ステップを紹介します。
いきなり大きな投資はせず小さく始めて、効果を確かめながら広げていく中小企業でも実現できるIoT導入の方法をチェックしましょう。
ステップ①|現場の課題を“数字”で見える化
まずは現場の悩みを洗い出し、改善の余地を数値で表現しましょう。たとえば「月30時間のムダ稼働」や「不良率8%」など。これが投資判断の土台になります。
ステップ②|成果を測るKPIを設定
洗い出した課題に対して「設備稼働率」「不良率」「エネルギー消費量」などのKPIを設定します。効果を定量的に評価し、PDCAを回すために不可欠な工程です。
ステップ③|PoCで小さく始めて効果検証
いきなり全社導入せず、1ラインや1台の機械から始めましょう。PoCなら数十万円から実施可能。投資リスクを抑え、現場の反応も確認できます。
ステップ④|成果を見せて全社展開へ
PoCの効果が確認できたら、ダッシュボードなどで成果を社内に共有。納得感が得られれば、他部署への展開もスムーズに進みます。
よくある失敗:「いきなり全社」「現場不在」「目的不明」
この3つの失敗は、PoCと現場巻き込みを丁寧に行うことで回避可能。小さく始めて成果を見せる──これがIoT成功の王道です。
6 まとめ|IoTはコストではなく“利益を生み出す設備投資”である
IoT導入は、初期費用や運用コストがかかるため、投資に躊躇する中小企業も多いでしょう。
しかし、本記事で紹介した事例のように、IoTは単なる技術導入ではなく、中小企業でも実現可能な「利益を生み出す仕組み」です。
人手不足・原価高騰・属人化といった経営課題を、センサー×見える化×現場主導の組み合わせで確実に改善できます。しかも、始めるのに必要なのは100万円以下のスモールPoCだけ。
大きな成果は、最初の一歩から生まれます。IoTを「コスト」ではなく、「未来への投資」と捉え、まずは自社の課題に合った小さな導入から始めてみましょう。